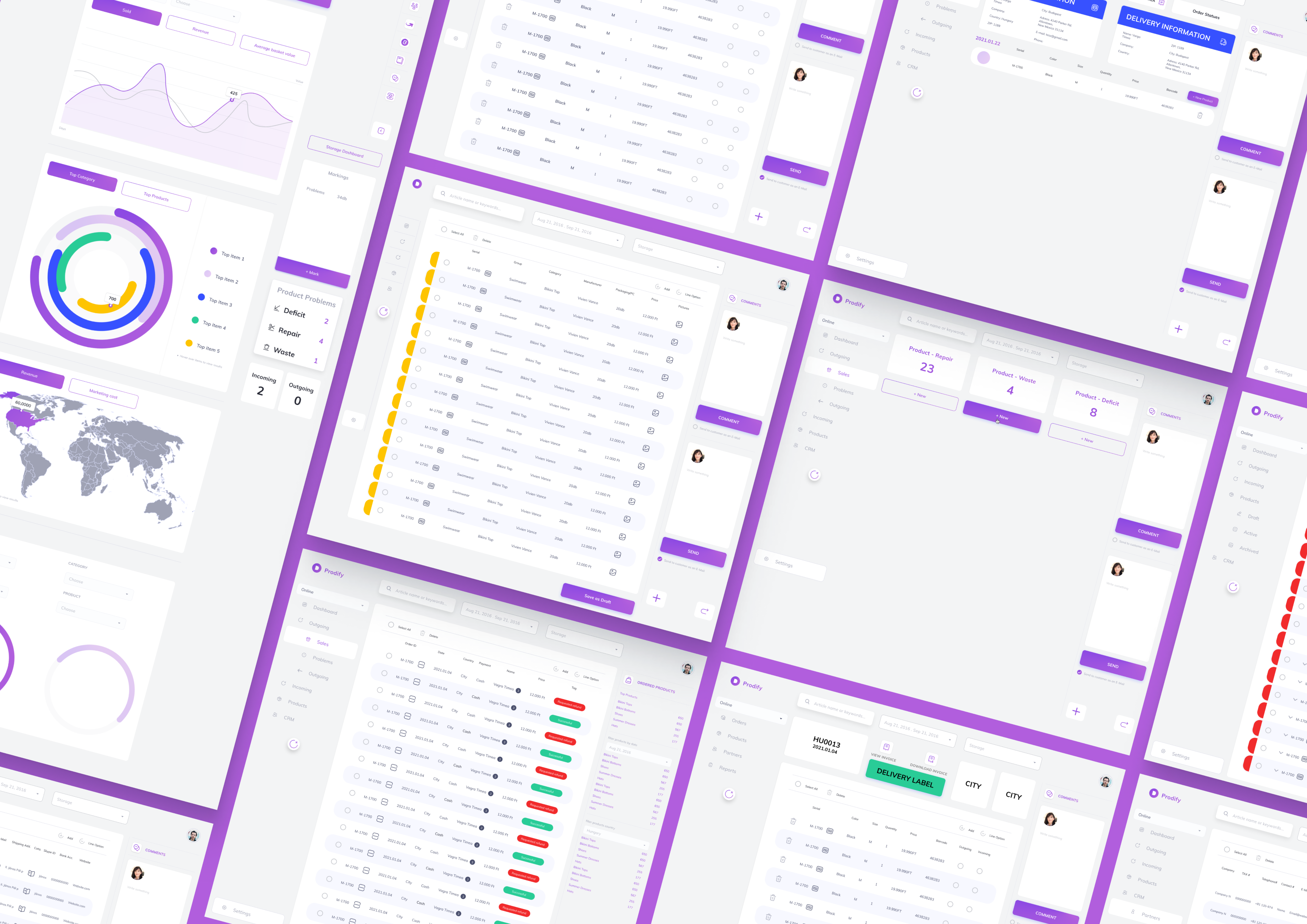

Development of Prodyflow webshop and logistics WMS
We designed and developed an online sales and business management platform for the clothing brand Vivien Vance. The company, called Prodyflow, handles the brand's warehousing operations across several countries.
We were tasked with everything from design to full implementation and live deployment, followed by the server-side services. Our joint work has continued ever since in terms of operations and maintenance services.
The collaboration between Vivien Vance and WebOrigo started in 2021. Our first task was to assess and prepare the project, which took almost six months. The development of the specification, which was based on preliminary surveys, was able to proceed much more smoothly because it was based on solid foundations. Working together, the aim was to build on all the components to ensure speed and efficiency, and to create a logical system for each component. The specification included the production of wireframes, flowcharts and the Figma visualisation design.
As a result, a modular software was designed and delivered during the 2 years of development. The aim was to enable any third-party software developer to create plug-ins to control the central system once the system was delivered. We ourselves built the system from such plugin components and delivered it with 40+ developed plugins providing solutions in the areas of invoicing, payment, logistics (mainly API services like DHL, GLS, Stripe). So, if you want to implement a new service provider or partner, a new reporting functionality, either a proprietary application developer, a third party or of course WebOrigo itself can develop a plugin to further extend the functionality of the system. Any such plugin functionality can be turned on and off by the superadmin.
The software is built up of 5 main elements:
- Inventory and warehouse management, logistics: this internal interface is the core of the software. Inventory information is the basis of the entire management and enterprise management process, as the system has built-in automation and algorithms that automatically place low, high stock levels into production or ordering. In the logistics module, the individual web shops, physical points of sale, warehouses and fullfillment stores can be managed separately, with the same defined minimum stock levels, packaging units, dynamic price management, and are all easily accessible and easy to overview.
- Sales: sales are made from this internal interface. Vivien Vance has physical outlets in several countries, whose sales are entered into this central system and can be easily tracked by the head office.
- Production: this internal system function monitors the production process. Purchase Orders (POs) can be placed through the interface and are fulfilled by the in-house sewing shop or other suppliers. The status and the time required for production can be tracked, and the sewing manager can also measure the efficiency of the sewing operators by monitoring the standard time.
- Webshop interface: the online sales interface (webshop) where the customer can order, add to cart and pay for their order. Here, too, innovative methods have been implemented, such as a password-free user account and the implementation of customer service-free exchange and return functions. After the purchase, the user can decide what to return and what to replace, thus drastically reducing the customer service workload.
- Mobile application: the mobile application is a React Native based application running on iOS and Android devices. It supports warehouse receiving and packaging, as well as stock control, as all devices can stay in real-time sync with the central system. The improved app helps to keep logistical errors to a minimum.
Project’s gallery
Check out next
Sign up for our newsletter!
Sign up for our newsletter to be the first to know about our latest projects and technological innovations.